
Category: Resources
Launch of The Amader Kotha Helpline Worker Training Video
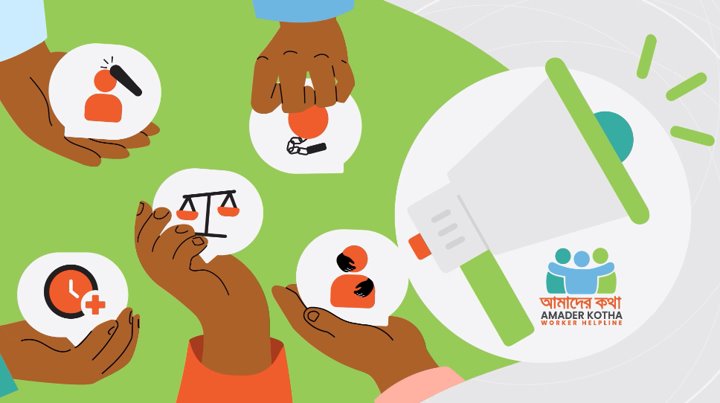
Creating awareness and trust of workers is critical to the operation of an effective grievance mechanism. In order to achieve this objective, information about how to use the grievance channel must be widely available and it must be presented in a culturally appropriate, relevant, and engaging way.
We are pleased to announce that the Amader Kotha Helpline in Bangladesh has recently developed a new animated worker training video as a next step in our efforts to support a high level of worker awareness and trust. The video provides workers with detailed information about how to access the Helpline and what to expect when a worker calls to report safety or labor related concerns in the workplace. It serves as an additional tool to complement our printed posters, cards, and stickers as well as our in-person trainings when requested. The video is available in English and Bangla.
We encourage you to take the time to watch the video as part of our ongoing efforts to provide information about the Helpline and how it can support safe and decent working conditions in Bangladesh.
Eid Helpline Hours
Dear All,
We hope this finds you in good health and high spirits. We would like to inform you that our Phulki office and Helpline Stations will be closed from 27th June to 4th July 2023 in observance of the Eid-ul-Adha holidays. Our operations will resume on 5th July 2023.
As a result of the holiday period, all factory operations in will also be temporarily suspended during this period. However, we will have an Emergency Contact Information/number available via our Helpline call recording service, which will be activated during the holiday period.
Wishing you all Eid Mubarak ! May this Eid bring you and your loved ones joys, happiness, and prosperity.
A New Logo for the Amader Kotha Helpline
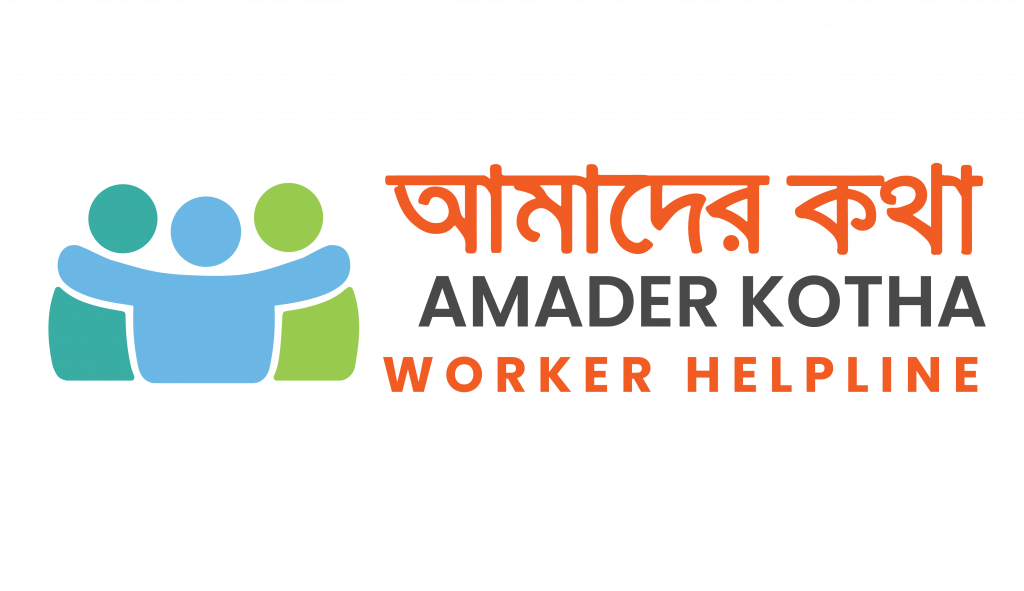
We are pleased to announce that the Amader Kotha Helpline in Bangladesh has updated its logo. As part of our ongoing commitment to improving the worker experience and promoting workplace rights within the RMG sector, we wanted to refresh our brand identity and give it a more modern and inclusive look.
Our new logo features three people arm-in-arm, representing the value and strength of worker voice in Bangladesh. The new logo reflects our belief in the importance of collaboration and community in addressing workplace issues. When designing our new identity, we surveyed workers to gather their feedback on several different designs to understand which design they felt most connected to, while maintaining strong brand recognition to the Helpline.
We believe that our new logo will help us better connect with workers and communicate the importance of their voices in the grievance process. We know that workers in Bangladesh often face significant challenges in speaking up about workplace issues, and our goal is to create a safe and supportive environment where they can be heard, have their challenges remediated and their rights protected.
At the same time, we recognize that a logo alone is hardly sufficient to create lasting change. We remain committed to working with our partners and stakeholders to build a more just and equitable RMG sector for all workers in Bangladesh. This includes providing training and support to workers and collaborating with employers to improve working conditions.
We’re excited to roll out our new logo and look forward to continuing our work to build a safer garment industry for all workers.
Q1 2023 Newsletter
Ensuring fashion supply chain grievance mechanisms are truly effective
The well-intentioned efforts of fashion brands and retailers to put in place grievance mechanisms in their supply chains are missing the mark. Companies should consider sector wide approaches, writes corporate responsibility consultant, Doug Cahn.
This article was first published on 4th May 2023 by JustStyle and was republished here with permission. You may find the PDF version here.
When John Ruggie, special representative to the UN secretary general for business and human rights, conceptualized the foundational principles for effective grievance mechanisms throughout the supply chain he understood the central role that fashion brands and retailers would play. He called on companies to ensure access to those mechanisms be a part of a company’s commitment to respect rights. When it came to operational-level grievance mechanisms in particular, he understood that a company’s obligations could be administered not only by each company acting alone, but by companies in collaboration with others. This is relevant for global brands today as regulators in Europe and elsewhere require transparent communications that document the impact of brands’ initiatives to protect workers in their supply chains, including their grievance channels.
Do grievance mechanisms for fashion supply chain workers work?
Leading fashion brands and retailers have invested significant time and money into developing and implementing global grievance mechanisms in their own supply chains. These efforts are well known and include reporting channels accessed through links to web forms, mobile apps, toll free numbers staffed by local compliance professionals or call centers. Information when provided by workers is managed in a variety of ways, each according to the customized protocols typically developed by the brand or retailer.
Evidence of these efforts can be easily found by glancing at a factory’s notice board where multiple customer hotlines can be found posted side-by-side, often creating a bewildering and confusing array of numbers to call or text in order to file complaints. Most are placed within sight of a watchful management who are suspicious of the role of third-party complaint channels and who passively or sometimes actively discourage their use. Workers rarely understand what to expect if they file a complaint and even more rarely trust management claims to refrain from retaliatory behavior.
To consider a better design of grievance mechanisms, we must first recognize two important truths:
- The unskilled and semi-skilled labourers that constitute the vast majority of the workforce in fashion supply chains are transient and their skill sets are fungible. They may work in one factory today and another factory next month or next year. This is the nature of a workforce that has recently entered the formal sector, is building skills, and is looking to better themselves and their families through higher skilled jobs and increased earnings. A worker who learns about a grievance channel in one factory may not be permitted access to it when they move to a different factory. This lack of continuity leads to a lack of awareness and trust.
- Factories and the subcontractors they use are rarely exclusive to one brand or retailer customer. As such, brand and retail-centric initiatives can appear to workers to be duplicative, confusing, or simply irrelevant.
Providing effective grievance mechanisms for garment workers in the long-term
Brands and retailers considering approaches to meet Germany’s new Corporate Due Diligence Obligations for the Prevention of Human Rights Violations in Supply Chains Act, for example, should keep in mind that investments in grievance mechanisms that are focused solely on a particular company’s supply chain may well meet their immediate reporting obligations.
However, effectiveness over time is not likely to be achieved unless grievance mechanisms are designed to reflect the transient nature of the workforce. In the complex web of commercial relationships between brands, retailers, suppliers, factories and subcontractors, workers do not fall neatly into brand-by-brand silos. Collective actions are needed and they are possible.
The Amader Kotha Helpline in Bangladesh serves as an example, supporting a significant portion of that country’s Ready-Made Garment (RMG) sector since 2014. As a partnership between Clear Voice, a project of The Cahn Group, ELEVATE an LRQA Company, and Phulki, a non-profit organization based in Dhaka, the Helpline has been able to provide in-factory training to over a million workers and currently provides a grievance reporting channel to over 400 factories. In so doing, the Helpline has become a one-stop shopping solution for workers who need to report and resolve a concern.
The benefits of this critical mass approach are many including:
- Reduction of confusion on the part of factory management and workers that comes with elimination of multiple brand and retailer grievance channels
- Widespread awareness of and access to the Helpline: workers will know or have heard about a friend or family members who have used the grievance channel
- Facilitating the ability of brand and retailers to collaborate on remediation when that is needed, consistent with anti-trust requirements.
Brands and retailers need not worry that collective or consolidated grievance mechanisms will make it difficult for them to exercise their responsibilities or deny them what they need to meet regulatory requirements. On the contrary, collective efforts will increase effectiveness and efficiency at the same time. Through agreed-upon escalation protocols, brands and retailers can learn of small problems before they become more serious or larger problems that require their timely attention.
Sector-wide initiatives take time to establish since they involve multiple parties aligned to a single set of operational protocols. Still, collaborative approaches that recognize and reflect the needs of a sector-wide labor force, and not the immediate fashion supply chain specific workforce, will be worth the effort.
Q4 2022
Q2 2022
